Digitaliserad och anpassad för hemsidan av Ray Beaufoy 2023-01-04
Maskin för helautomatisk motorblocksbearbetning installerad i år. Utför 25 arbetsoperationer.
I Saabs motorverkstad i Göteborg har bolaget investerat totalt omkring 90 miljoner kronor, varav cirka 30 miljoner under de senaste tre åren. Detta bland annat omtalade direktör Svante Holm vid en pressvisning av verkstäderna i oktober. I visningen som var den första för rikspressen, deltog ett 40-tal journalister från dags- och fackpress
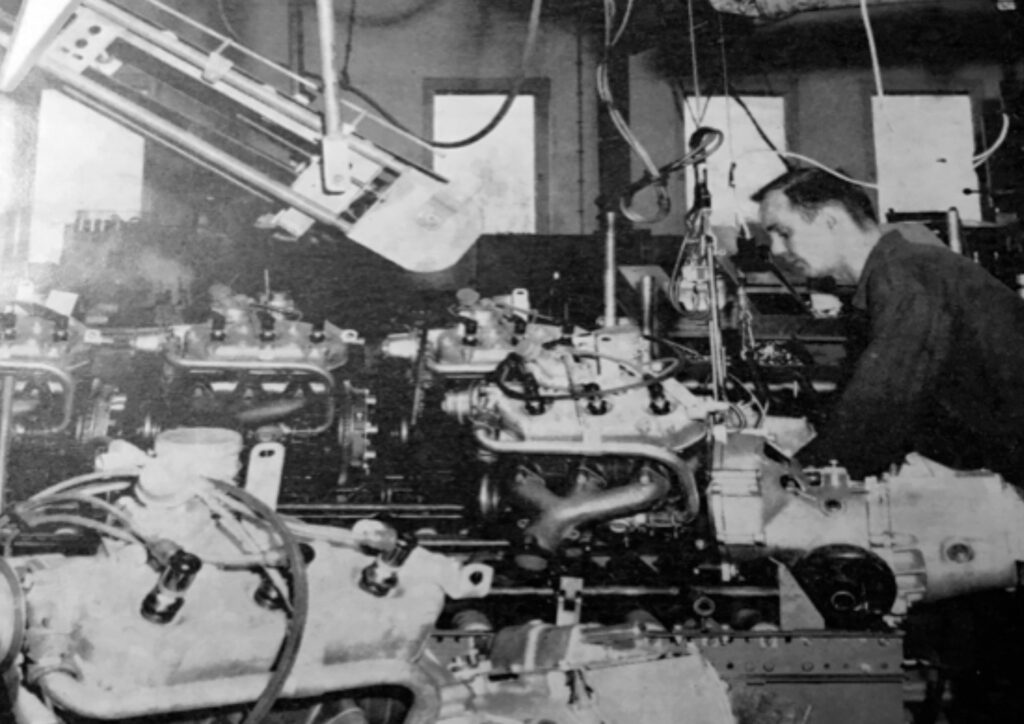
Saab har inga planer på att gå ifrån tvåtaktaren, sade direktören Holm vidare. Ett uppenbart bevis på detta är de betydande maskininvesteringar, cirka 3miljoner kronor, som nyligen gjorts på motorblockslinen. Däri ingår den i år installerade s.k. transfermaskinen, som bland annat automatiskt utfört 25 arbetsoperationer. Maskinen är specialbyggd för Saabmotorn och praktisk taget omöjlig att ändra för tillverkning av en fyrtaktsmotor.
För att komma till rätta med oljeröksproblemet kommer Saab ej att välja separatsmörjning eller oljeautomatik, upplyste överingenjör Rolf Mellde under pressinformationen. I samarbete med flera oljebolag pågår intensiva prov för att få fram en specialolja för magrare inblandning i bränslet och därmed minskning av både rök och lukt.
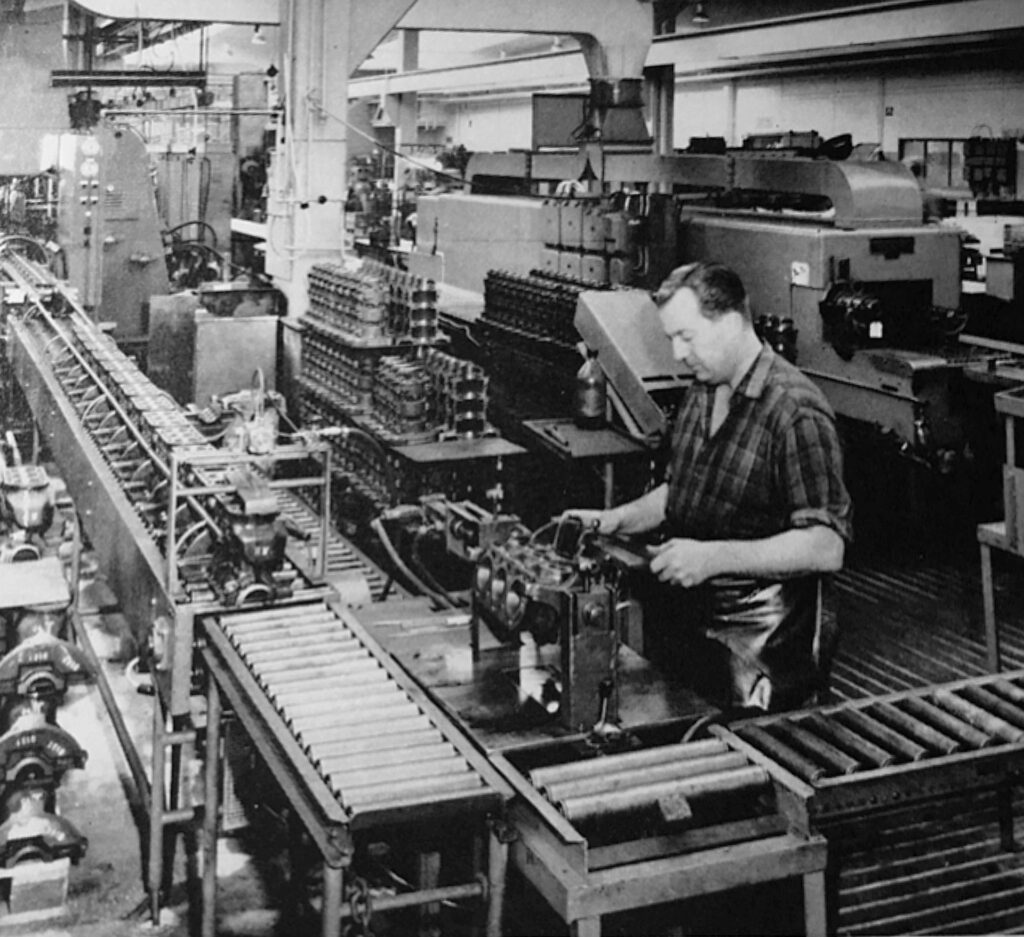
Tiodubblad produktionsökning på tio år
Det är nu tio år sedan Saab började tillverka motorer och växellådor i Göteborg.1953 köptes de dåvarande verkstadslokalerna av Electrolux och påföljande år kom tillverkningen i gång. Vid tillträdet var fabriksgolven 16.000 m2. I dag är den närmast fördubblad, eller 30.000 m2.
1954 tillverkades 4.000 drivaggregat (motor/ växellåda) per år. Förra året var produktionstakten 10 gånger högre och i november i år når man 50.000-takt.
Denna våldsamma produktionsökning har till stor del möjliggjorts genom en pågående arbetsrationalisering. 1954 krävdes sålunda för framställning av ett drivaggregat 37 arbetstimmar medan det i dag fordras endast 10,2. betstimmar.
Antalet anställda vid Saab-G är i dag cirka 750.
Verkstadsområdet färdigbyggt
Genom ökning av maskinparken kan en ytterligare stegring av produktionen ske till 60.000-takt. Detta är dock gränsen med nuvarande verkstadsanläggningar, som i.o.m. färdigställandet av det nu påbörjade parkeringshuset för anställdas bilar (beskrivit i VIPS nr 3/64) är helt utbyggda. För tillverkning av fler än 60.000 drivaggregat per år fordras nya fabrikslokaler.
Utbyggnaderna av verkstäderna har pågått successivt och omfattar både renoveringar och nybyggnader. Senaste färdig är den 160 m långa och tre våningar höga fabriksbyggnad som helt tagits i bruk i början av detta år. Byggnadskostnad cirka 10 miljoner kronor.
I denna byggnad tillverkas huvudsakligen växellådor. Där sker bearbetning av kugghjul, axlar, etcetera, liksom montering och provning av lådorna samt sammontering med motorenheten.
Tillverkningsförlopp
Tillverkning för motorer och växellådor går enligt följande förlopp…
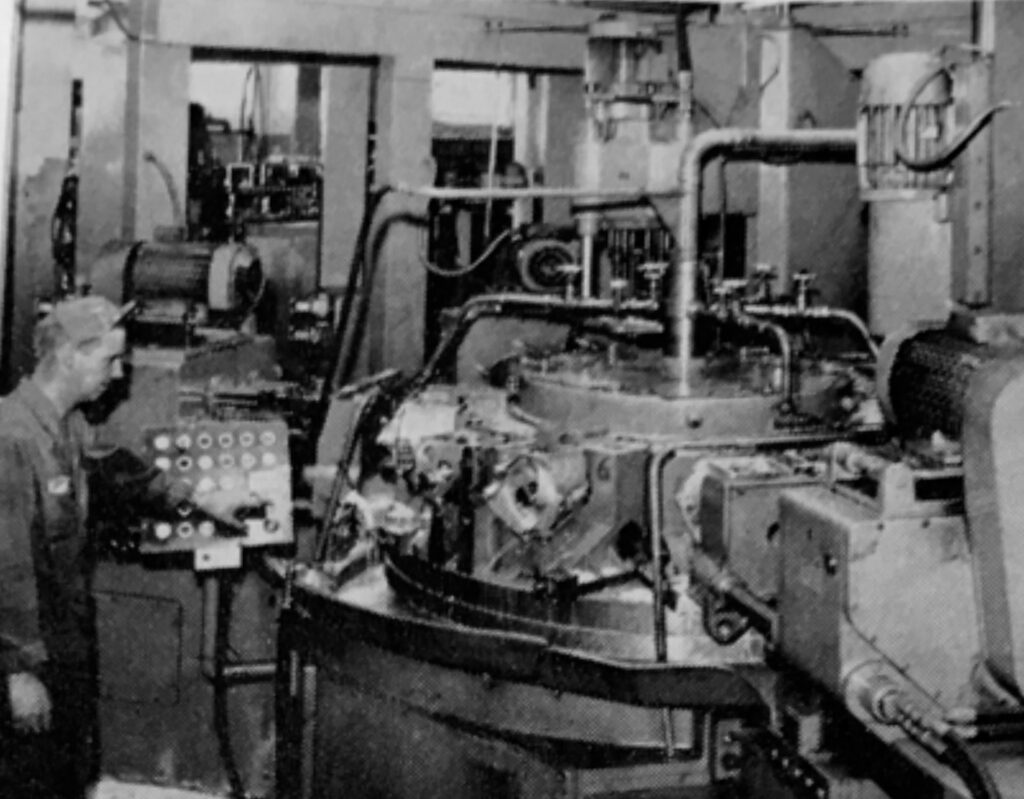
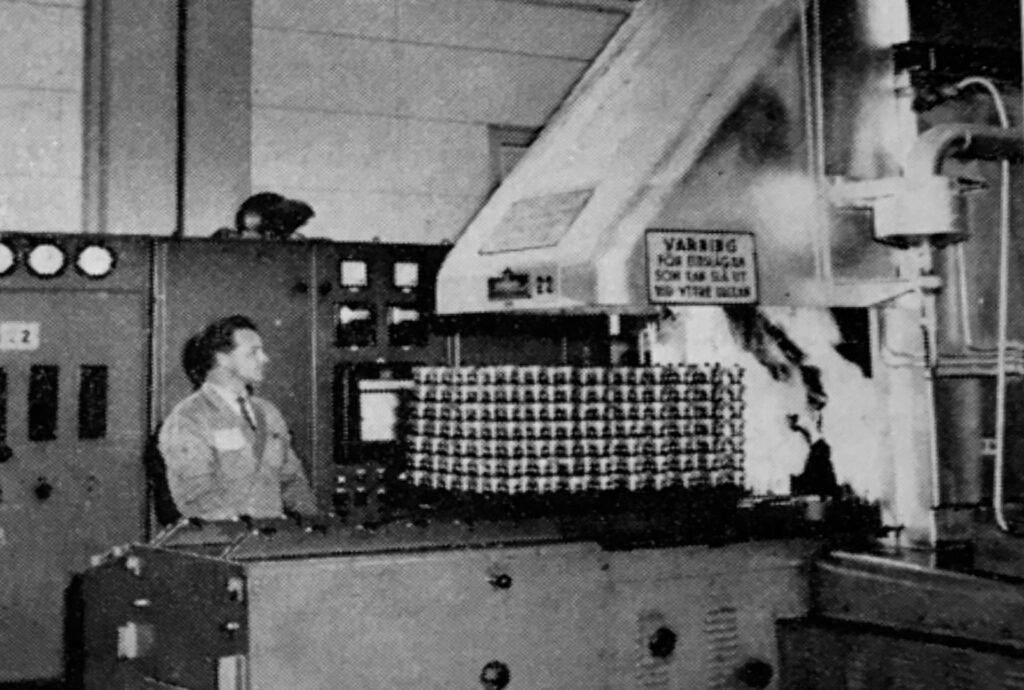
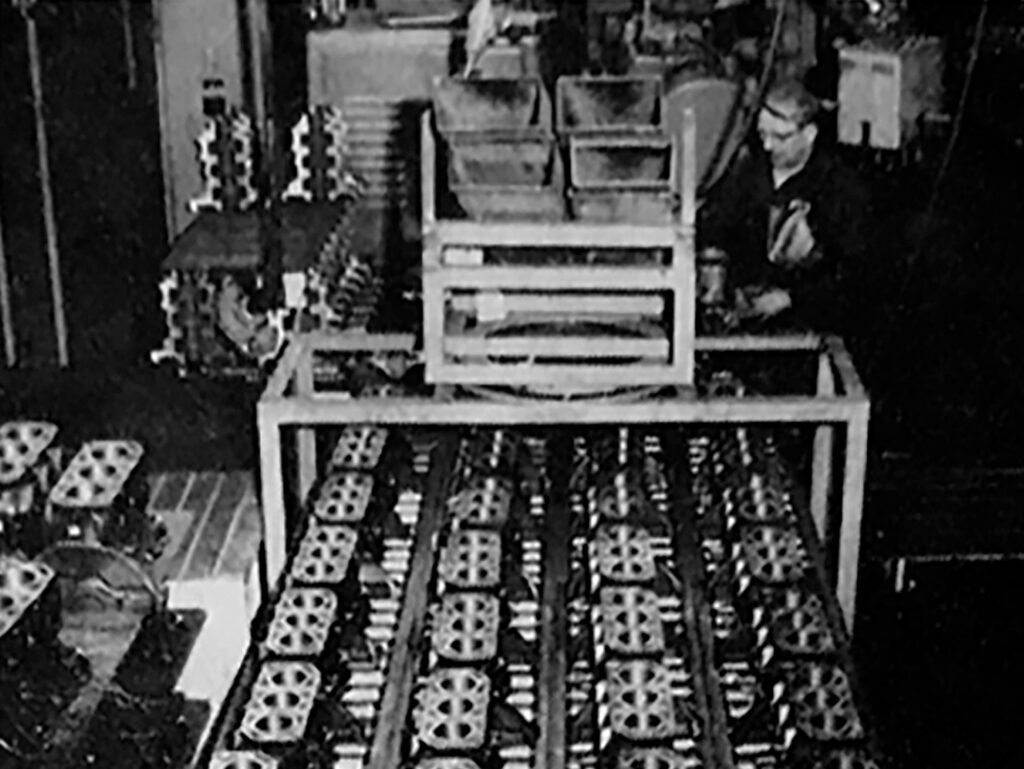
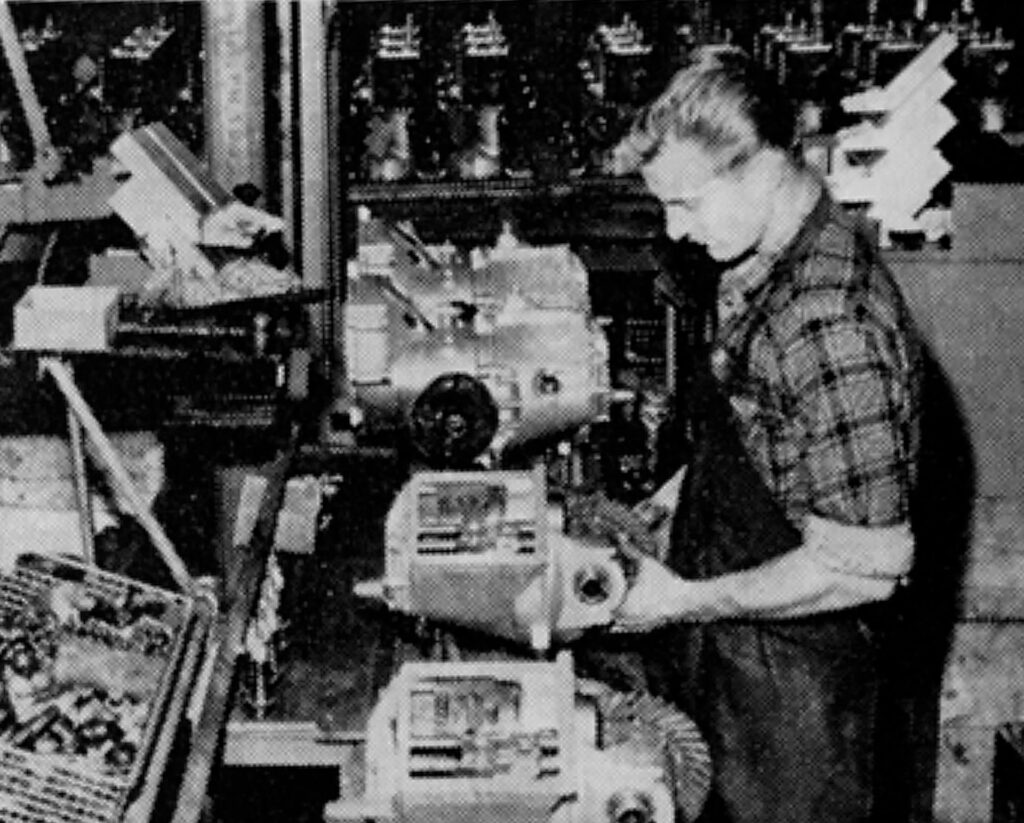
Innan tillverkningsproceduren startar, genomgår råmaterialet en omfattande ankomstkontroll. Den omfattar såväl materialegenskaper som dimensioner och avser att verifiera att till bearbetning endast går sådant material som uppfyller fordringarna enligt gällande specifikationer. Kvalitetskontrollen är för övrigt en utmärkande faktor vid tillverkning av Saabbilen. Även under det fortsatta tillverkningsförloppet utsätts detaljerna ideligen för olika kontrollmoment, och i runda tal var sjätte anställd vid Saab-G har en kontrollfunktion av något slag.
Flytande tillverkning av större detaljer
Sedan materialet passerat kontrollinstansen, levereras det till förråd och går därefter ut till bearbetning. De större gjutgodsen, så som växellådskåpa, motorblock, och kopplingshus, bearbetas i speciella maskingrupper, s.k. ´lines´, där en rent flytande tillverkning tillämpas, dvs en detalj överflyttas, så snart den är klar in en maskinoperation, till nästkommande operation. Transporterna sker på rullbanor och några längre liggtider förekommer inte.
LLängst driven är tillverkning av motorblocket. Här används den tidigare omnämnda transfermaskinen, där blocket helt automatiskt transporteras från arbetsmaskin till arbetsmaskin och passerar 25 arbetsstationer utan någon som helst manuell betjäning.
Mannen i maskingruppen närmast före transfermaskinen har endast att efter sin operation mata in blocket i transfermaskinen, efter transfermaskinen har endast att efter sin operation mata in blocket i transfermaskinen, varefter mannen i maskingruppen närmast efter transfermaskinen har att ta emot det färdigbearbetade blocket för sammanbyggnad med vevhushalva och vidare bearbetning. I transfermaskinen finns således i arbete 25 block, och maskinens takttid är 1 ½ minut, dvs. det tidsmellanrum med vilket blocken matas ur maskinen.
Totalt antal arbetsspindlar i maskinen är 127 och de flesta arbetsstationerna i maskinen har kontrollorgan som dels kontrollerar att närmast föregående stations operationer verkligen är utförda – dels också kontrollerar att bearbetningsverktygen är oskadda och i fullgott skick.
I transfermaskinen fräses på varje block 4 plan, 75 hål borras, av vilka 40 gängas och 8 brotschas.
Varje enhet protokollförd
Maskinkapaciteten vid de olika bearbetningsstationerna vid s.k. linjetillverkning har avvägts så, att arbetsmomentet vid varje station är tidsmässigt i det närmaste lika långt. Stationstiden står helt i samklang med och styrs faktiskt efter takten vid monteringslinan för den kompletta bilen vid fabriken i Trollhättan.
Under tillverkningens gång kontrolleras genom stickprov, att de bearbetade dimensionerna ligger inom föreskrivna toleransområden. Tendenserna i måttförändringar studeras och med ledning härav görs erforderliga justeringar för slitage på bearbetningsverktyg och fixturer. Mycket noggranna mått, exempelvis lagerpassningar för ramlagren i cylinderblocken respektive cylinderloppen i dessa, genomgår en särskild finborrningsoperation med efterföljande honing av ytorna. Här mäts och protokollförs varje enhet.
Klassade cylinderlopp.
För att motorn skall kunna innehålla det rätta kolvspelet – totala spelet mellan cylinderlopp och kolv – är det nödvändigt med noggrann mätning och klassning av cylinderloppen respektive kolvarna. Cylinderloppen klassas i olika grupper med toleransområdet 0,007 mm. Kolvarna, som köps färdiga, levereras klassade i 4 grupper, medan däremot klassning av cylinderloppen sker i samband med slutkontroll av blocken vid blocklinen.
Klassningen sker i en speciell mätmaskin, där mätkolvar automatiskt går ner i loppen och på ett tillhörande mätinstrument anges respektive klass för de tre cylinderloppen.
Cylinderblocken får vidare genomgå en täthetsprovning för att kollationera, att läckage ej förekomma från vattenmanteln. All bearbetning avslutas med en tvättningsoperation innebärande avfettning och rengöring av detaljerna, innan dessa går till förråd.
Smiden och stångmaterial i stål, som i huvudsak ingår i motorns vevaxel och i växellådans kugghjul och axlar, har en i stort likartad operationsföljd, i det att maskinbearbetningen som regel följs av en härdningsoperation med efterföljande slipning.
De första tillverkningsoperationerna sker som regel i halvautomatiska svarvar med kamstyrda eller kopierande förlopp. Tillverkningscykeln omfattar flera olika operationer och maskinskötaren har endast att sätta upp detaljen samt ta ut den, när tillverkningsförloppen är avslutat.
Under senare år har fräsning i stor utsträckning ersatts med yt- eller och dragbrotschning, dvs. materialavverkningen åstadkoms förenklat genom att en stång med stort antal fräständer förs fram över materialet. Sålunda dragbrotschas vevskivornas båda sidor, vevstakens sidor, hålet för vevlagret mm.
Sedan detaljerna svarvats, sker när det gäller kugghjul och axlar, någon form av kuggskärning. Detta utförs alternativt som kugghyvling eller avvalsningsfräsning i maskiner av modernaste snitt. De flesta av dessa maskiner är försedda med laddningsmagasin och inrättade för automatiska omladdningar. En sådan maskin kan efter laddning lämnas i full produktion utan tillsyn för en tid av 1–2 timmar. Detta möjliggör att en man kan betjäna flera maskiner och antalet maskiner i de enmansbetjänade grupperna uppgår till 4–7.
Härdning och slipning
Av flertalet detaljer krävs, att de skall ha hård yta och seg kärna. De skall vara hårda och oömma för ytligt slitage men sega inuti för att stå emot dynamiska påkänningar. Hårdheten åstadkoms genom s.k. sätthärdning alternativt induktionshärdning.
Sätthärdningsproceduren innebär, att detaljerna under viss tid förvaras i en ugn vid en temperatur om ca 900 grader. Härvid omspolas de med en kolavgivande gas och ytskiktet uppkolas. Uppkolningsmomentet följs av härdning i oljebad och därefter anlöpning vid en temperatur av storleksordning 150–160 °C. Nyligen har en s.k. kontinuerlig gasinkolningsugn installerats, där momenten sker automatiskt efter varandra utan manuell hantering eller övervakning.
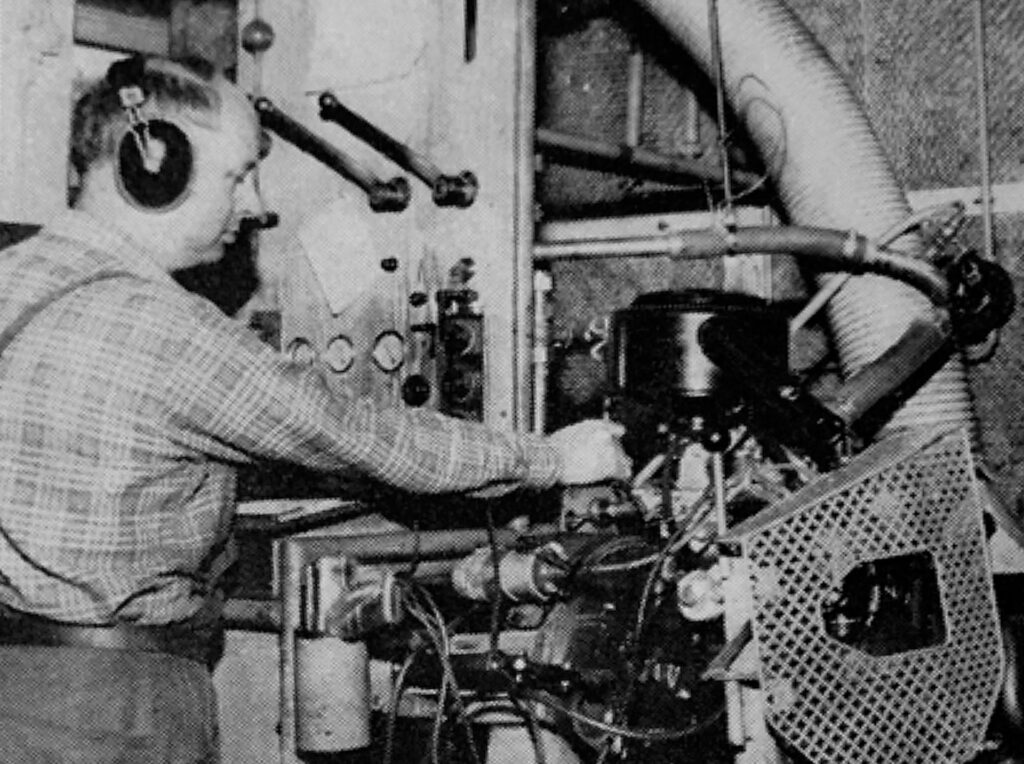
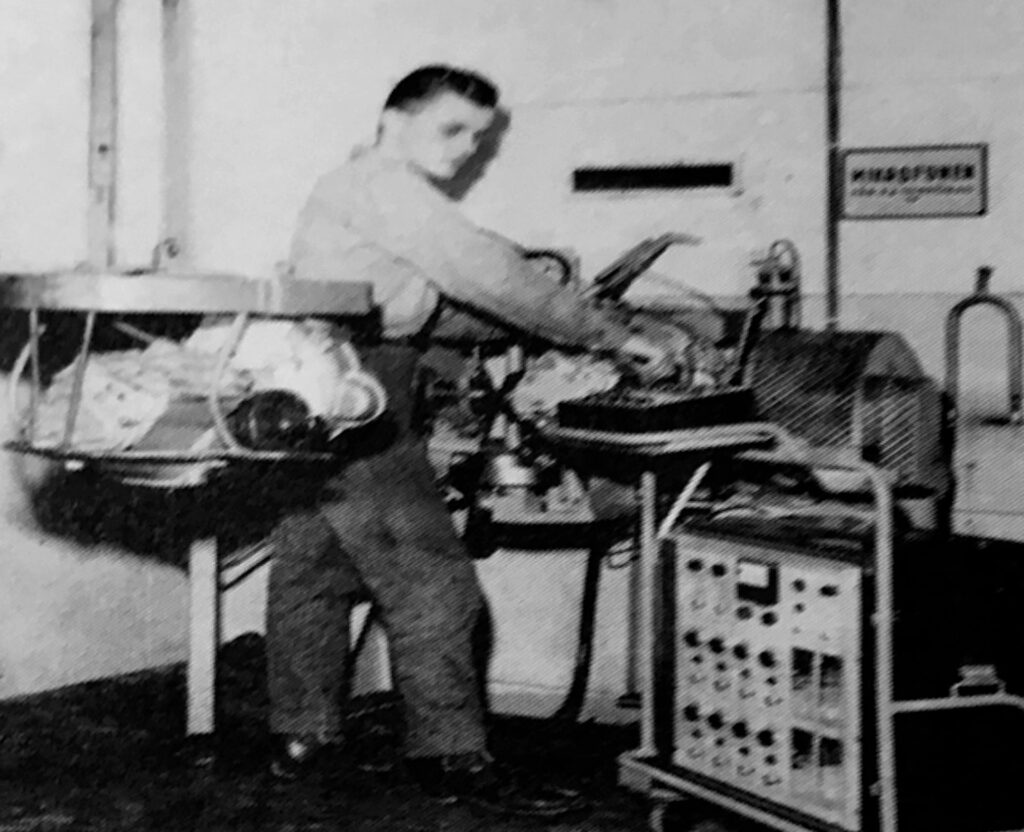
Ugnen är också försedd med automatisk inmatning och utmatning av detaljerna och kan efter full uppladdning med detaljer sköta sig själv utan tillsyn under cirka 20 timmar.
Induktionshärdning innebär att detaljerna placeras i ett specialaggregat och uppvärmas induktivt. d.v.s. de av aggregatet åstadkomna elektriska virvelströmmarna i detaljen ger en tillräcklig uppvärmning för den erforderliga härdning som sker omedelbart genom vattenspolning i härdaggregatet.
Parade växellådshjul
Samtliga härdade detaljer slipas på blivande lagerytor eller där någon annan form av passning mot annan detalj krävs. På kugghjulen slipas dessutom kuggflankerna för att korrigera formen med hänsyn till eventuella härdförändringar. Detta är särskilt angeläget på 3:ans och 4:ans växlar, där kravet på låg ljudnivå är högt.
Efter slipning följer för kugghjulen en särskild parnings- och ljudprovningsoperation för de olika växlarna.
Ett genomgående drag för hela bearbetningen är, att den avslutas med en slutkontroll, som innebär en uppmätning av vitala mått liksom kontroll av hårdheten.
Motor och växellådor monteras på löpande band
Motor och växellådsmonteringen sker efter löpande bandets princip.
Växellådsmonteringen startar med sammanbyggnad av axlar och kugghjul, med andra ord växellådans innanmäte placeras på plats. Detta sker i en monteringsbana, där i olika stationer de yttre detaljerna såsom gavellock, växelförarlock, inre drivknutar med mera monteras. De olika monteringsmomenten utsätts för en ständig stickprovskontroll beträffande kuggväxlarnas flankspel med mera.
Den kompletta växellådan transporteras på automatiska taktransportörer fram till ett växellådsprovrum för växellådsprov analogt med driftsförhållandet i bil.
Växellådsprovbänkarna är kringbyggda med ljudabsorberande väggar för att medge en korrekt ljudavlyssning. Provbänkarna är också försedda med fastsättningsanordningar för växellådorna, vilket medger drivning och belastning under samma betingelser som i bil.
På varje bänk finns två skivbromsar en för vardera drivaxeln. Bromskraften kan varieras med hand eller fotreglage. Provbänken drivs från en i ett intilliggande rum placerad el-motor via en mellanliggande elektromagnetisk slirkoppling. Denna medger en steglös reglering av lamellaxelns varvtal.
Växellådan avlyssnas
Ett första led i provningen är funktions- och ljudprov på samtliga växlar. Provet utförs vid varierande varvtal och belastning. Ljudnivån bedöms i förhållande till en speciell masterväxellåda eller kontrolleras med elektronisk mätapparat som kalibreras efter masterlådan. Frihjulets och differentialens funktion kontrolleras även i samband med detta prov.
Under provet innehåller växellådorna olja som samtidigt tjänstgör som sköljolja. Denna avtappas sedan och filtreras efter provet. Den godkända växellådan fylls med ordinarie växellådsolja och levereras vidare för sammanbyggnad med motorn.
Utöver detta funktions- och ljudprov, som varje växellåda får genomgå, utförs även en tioprocentig kontroll av växlingsmomentet och en femprocentig kontroll av ljudnivån på kuggväxlarnas baksida (de kuggflanker som är belastade när bilen rullar utan drivning från motorn). Utöver detta uttages cirka var 300:e växellåda för körning med max. tillåten belastning i en s.k. långtidsprovbänk.
Dammskyddad transporttunnel
Montering av motorn startas med, att vevaxeln hopbyggs. Den består som bekant av tappar och skivor, vilka pressas ihop. Ett särskilt noggrant moment härvid är valet av rullar för vevlagret, och rullarna väljs efter en speciell mätoperation. Rullarna levereras av SKF och är klassade på 0,0005 mm. Den kompletta vevaxeln inläggs i en särskild, dammskyddad transporttunnel. Vevaxeln är lagrad i kullager och vevstakarna som nämns i rullager, och det är synnerligen viktigt, att några föroreningar ej kommer in i lagerbanorna.
Den fortsatta monteringen sker efter löpandeband-principen med olika arbetsmoment stationsvis utplacerade fram till den kompletta motorns transport till provrum.
Till den hopbyggda vevaxeln monteras kolvar motsvarande de klasser som finns angivna på det aktuella cylinderblock, som står i tur att förses med vevaxel. Därefter följer fastsättning av svänghjul, cylinderblockspackning och topplock samt vidare montering av insugningsrör med förgasare och avgassamlare samt tändfördelare.
Direkt från den sista monteringsstationen i monteringslokalen transporteras motorerna stående i speciella ställ till provrummet.
Motorprovning i bänk
Provrummet är indelat i provceller med två motorprovbänkar i varje cell. Av praktiska skäl utför en provare en samtidig provning i ett sådant provbänkspar. För att möjliggöra avlyssning av motorerna har provrummets väggar och tak klätts med ljudabsorberande rockwollmattor.
Motorprovbänkarna är utrustade med vattenbroms för bestämning av den provade motorns effekt.
Sedan en motor inkopplats i provbänken, startas den för inkörning under sex minuter. Under inkörningen kontrolleras även tändinställningen med särskild tändinställningslampa. Efter inkörningen kontrolleras motorns specifika bränsleförbrukning vid 3.000 varv per minut med fullt öppet trottelspjäll. Ljudnivån avlyssnas och tomgångsinställningen finjusteras. Samtliga provvärden jämte lufttemperatur och barometerstånd noteras i provningsprotokoll.
Då motorprovet avslutats rostskyddsbehandlas (konserveras) motorn invändigt genom att en kvantitet olja tillförs genom förgasaren.
Utöver denna provning, som utförs på varje motor, uttages omkring var 300:e motor för ett fullständigt effektprov, som då föregås av en omfattande inkörning (5 timmar). För motorer till Saab Sport är inkörning respektive fullständigt effektprov obligatoriska.
Sammontering motor-växellåda
Den provade motorn och växellådan sammonteras och går därefter till kompletterande montering av el-utrustningen och är sedan klar för slutbesiktning och leverans per långtradare till Saab-Trollhättan. Leveransen är f.n. är 200 aggregat per dag.